タチエスが大切にしている『チームでのモノづくり』を感じていただけるように、社員同士の座談会を行いました。
今回はインテグラ(※)のシート開発に関わったプロジェクトメンバー4名に集まってもらい、当時の様子を熱く語ってもらいました。
(※)印の言葉はページ下部に補足内容を記載しています。
Talk Member
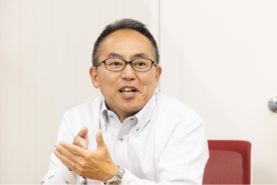
調達企画部
1990年入社
N.H(部長)
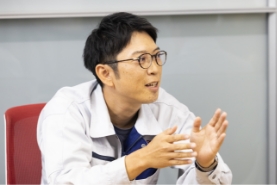
製品開発部製品設計課
2007年入社
N.Y(主任)
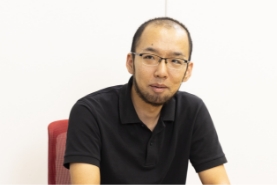
生産技術部軟材生産技術課
2010年入社
Y.H(主任)
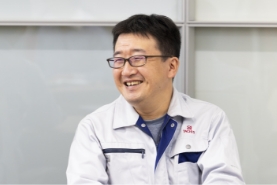
試作実験部実験評価課
2012年入社
S.K
プロジェクトのはじまり
このプロジェクトのきっかけは、Honda社より新規シート開発の提案機会をいただいたことでした。Honda社の期待を超えるべく様々な提案をした中の1つが、タチエス固有技術であるGlueAnchor®(※)だったのです。
アキュラ(※)ブランド独特のシートデザインパターンを再現できる技術として先方のニーズに適した提案に繋がり、タチエスでの開発を任せていただけることとなりました。
Talk Theme
01
大変だった点
導入の苦労

N.Y
このプロジェクトは、Honda社が北米展開するアキュラ(※)ブランドのクルマに搭載するシートで、日本で開発を完了し米国で量産展開するというプロジェクトでした。
いざプロジェクトがスタートし、シートデザイン形状の再現性や性能・品質目標達成に向けてHonda社との合同開発が始まりました。
量産化に向けた設計仕様の妥当性検証、それを具現化する工程工法を確立させる為、幾度も試作評価と解析を重ねたことはとても苦労した点ですが、これこそがモノづくりの醍醐味でもありました。

Y.H
量産実績がないものをいきなり海外に導入するっていうところが大変でしたね。
準備段階で現地のタチエス米国法人と1週間に1回の定例ミーティングで意見交換を行っていましたが、コミュニケーションの難しさ、意見の食い違いなどがあったり、メールで質問をすると回答を確認できるのが次の日になってしまうなど、様々な点でもどかしさがありました。
接着剤を使用してパッドの溝にトリムカバーを接着するこのGlueAchor®工法は世界初であることから、私たち生産技術部門も1から接着剤のことを勉強しました。現地メンバーにその工法、技術を教え込むところも非常に大変でした。

N.Y
日本での開発を完了し、満を持して米国での量産準備に移行した時のことですが、このGlueAchor®という技術の量産化は、世界初となるということで前例のないミッションにリスクと不安を感じるスタッフもいました。
それを払拭すべく、日本開発陣が自信をもって技術プレゼンを行い目標達成に向けて現地スタッフの安心感とモチベーションを引き出せたことはとてもいい経験になっています。

N.H
Honda社には「タチエス固有の技術です」というアプローチをしていて、タチエスの接着の技術があれば、競合他社と比較してデザインにすごく自由性があることを理解していただいた上で、今回の開発の採用に至っています。
デザインの再現性が高められるんだったら是非チャレンジしましょうという「モチベーション」を持ってもらえるよう米国法人に営業メンバーで力を合わせて説得に行きました。
その熱意が米国法人側のメンバーに十分に伝わったんだと思います。モチベーションを一緒の方向を向けられたというのが1番大きいと思います。
そして行動力というところも評価してくれたんだと思います。
これがもし、現地に行かずに机上や資料で開発を続けたとしたら、状況は変わらなかったと思いますね。
そのアクションをしたところが非常に良かったんだと思います。

N.Y
モチベーションを一緒の方向に向けたという点では米国エンジニアに対しても同様でした。
新しい技術を作り上げるだけでは無く、ノウハウの蓄積や確立した技術が強みになる事などポジティブな面を前面に出し熱く伝えましたし、
Honda社の期待に応える外観性能の達成技術であったり、今後の車種へ展開することで新規ビジネスの獲得にも繋げられると、特にアキュラブランドのある北米で、自社としての武器が備わるという点を理解してもらいました。
また、技術的には新しい技術・構造での初のチャレンジの為、設計の標準であったり管理ポイントを確立する事に試行錯誤でした。そういった中で品質を安定させるということが1番難しかったです。

Y.H
開発時に苦労した点は、これまで扱ったことのない接着材の特性を理解し、シートに求められるスペックを満足させるため、接着するときの条件を何パターンも試して1つ1つ接着条件を決めていったことです。
トライアンドエラーの繰り返しで根気のいる作業でしたが、チームメンバーと一番議論した時期で、思い返してみると一番楽しかった時期でもありますね。

N.H
量産化の難しさは、机上だけでは終わらない所なんです。
実際は試行錯誤を繰り返しながら収益も確保できるよう、そこは現場の開発メンバーには技術的に頑張ってもらいながらクリアしました。

S.K
とにかく普段の開発時とは違うやり方で実験する内容が多かったと思いますね。

S.K
性能評価に関しては、すべての完成車メーカーでも使えるように要求性能を満足させたい思いもありました。
様々な角度と目線で評価すれば、後々活きてくる技術ではないかと考えていました。
事前に、要素試験とシミュレーションで準備をバッチリやり切った状態で本番の実機テストに臨めたので、NGが少なくスムーズに評価できたのが良かった点ですね。

N.Y
試作実験部、要素技術開発部、生産技術部など様々な部署と連携しながらプロジェクトを進めました。
良かった点は、エラーが出た時、何が悪いかをみんなで一緒に冷静に考えられた点です。他責にするようなことがなかったですね。
課題を洗い出してそれぞれが対策して、良いものをチューニングしていくことができ、まさに「ワンチーム」を体現出来ました。
これができたことが本当に良かったです。

Y.H
設備は日本で準備しアメリカに輸送して導入したのですが、量産機を使用して実際に接着させたのはアメリカで初めて行なったんです。
日本で接着させるための要素をしっかりと研究していたので不安はありませんでしたが、今思い返すとドキドキですよね。
量産機で接着された製品を取り出して品質に問題ないことを確認したとき、先輩のHさんはそれを見て感動して涙を流し、米国メンバーと歓喜の声を上げたと聞いています。
私は出向準備のため一時帰国していたタイミングだったので、その場で感動を分かち合えなかったですが、結果を聞いたときは達成感を感じたことを覚えています。

N.H
営業担当としては、開発を始めて完成車メーカーへアプローチして、それが採用・開発されて、設備がアメリカに導入された写真が送られてきた時、本当にこれから現実になるんだと実感して嬉しかったですね。

S.K
開発時点でのテストは日本国内で行いましたが、今回は海外拠点で量産して、出来上がったものを現地でテストする流れになっていました。
その中で、日本はどうやってやったんだ?って聞かれるのが1番大変でしたね。
初の工法で作ったSEATなので、テスト方法について開発時に行ったテストの様子とか、どうやって作業をしたのかなど、現地とコミュニケーションを取りながら行き違いのないように伝えるのに苦労しました。
アキュラのインテグラ(※)は日本国内で売ってない車なんですよね。
海外サイトの新車紹介記事にシートが掲載されているのをインターネットで見つけたりします。
その時に、多くの方の目に触れるようになったんだなぁと思う時はやっぱり嬉しいですね。

Y.H
生産技術の視点で言うと世界初の工法なので、設備を1から自分たちで考えたところです。
金型の交換を自働化して段取りスピードアップ、人にやさしい設備という考えも織り込みました。
日本では取り扱いの少ないアメリカブランドの制御を入れる必要があり、制御設計者探しからのスタートでかなり大変でしたが、自分たちで構想した設備が形となり、スムーズに動かすことができた時はとても嬉しかったです。
Talk Theme
03
プロジェクトが
成功した理由

N.H
精根強くというかすぐに行動に移すというのが、今回はプロジェクトチーム内ですごくあったんじゃないかなと思いますね。
様々な部署と協力しながらコミュニケーションを取っていく事がすごく良いチームでした。

N.Y
試作実験部や要素技術開発部、生産技術部が試作TRY段階での検証を進んで実施し、造り込みに必要な材料を揃えて行ってくれたことでしょうか。
自ら責任を持ち自分たちの検証部分はやりきる、そこからブラッシュアップしていくという姿勢で、みんなで良い物を作っていこうという空気がひしひしと伝わりました。
皆さんポジティブ思考でしたね。ちょうど新型コロナウイルスが流行する前の良い思い出です。

S.K
実験だと業務で関わりが多い部署は製品開発部が多いですが、今回は生産技術部の方々とも関わることが多かったですね。
「試作品のサイズを変えて作ってもらえませんか?」みたいなやり取りが結構ありました。
色々話す機会があったおかげで、一気に人の顔と名前を知れたかな。
今回幅広い部署の人たちが動いているのを感じていたので、私だけでなく他の人たちも一気に人の輪が広がる感じがあったと思いますよ。

Y.H
日本で開発試作をしていた時期も量産機を米国に導入して設備準備していた時期も、何かあるとすぐにチームメンバーが集まって議論し、GlueAchor®工法を必ず成功させようという意識の高さを強く感じて心強かったです。
課題に1人で悩むことなく、チームが1つとなって取り組むことで早期解決出来ていたことも成功の要因の1つだと思います。

N.Y
GlueAnchor®を量産化したプロジェクトをやり遂げたチームに対して、社内で社長賞を貰えたんです。
やはりチャレンジをして良かったと言うのと、そういったチャレンジを評価してくれる会社であることを改めて感じさせられました。
また何か新しいことにチャレンジしたいというモチベーションができましたね。
またお客様からの評判も上々であるというお話も聞くことが出来ましたし、座り心地のプロフェッショナルなチームにも好評でしたね。
Talk Theme
04
今後の展望
未来に向けて

Y.H
今後の展望は沢山あります。
設備費、加工費などのコスト部分ではまだまだ改善できる余地があると思っており、設備サイズのコンパクト化、新しい接着剤への切り替え、省人化などやりたいことは山ほどあります。
お客様にも工場の方にもGlueAnchor®のシートを採用したい!この工場にも導入してよ!って言われるような技術になるようにもっと深化させていきたいです。

N.H
これから軽自動車とか国内外で多くの車種にも幅を広げていきたいですね。
そういうデザインの自由度だとかっていうのも付加価値として提案して、更なるビジネスにつなげていけたらなあって思います。

S.K
実験としては、このGlueAnchor®が多くのお客様の手に渡った時、良くも悪くも予想できないフィードバックが出てくると思います。
世界中には想像つかないような使い方をするユーザーさんもいるので、起きた事象に対応できるようなテスト方法を考える必要も発生すると思いますね。
そういったことも踏まえた上で先回りした評価等ができるように動ければベストかなと思うんですが、それは今後の課題ですね。

N.Y
GlueAnchor®を他拠点での採用に向けて奮闘中です。
その中で更にGlueAnchor®が深化し、お客様の要望以上の仕様が出来上がる様、今後も造り込んで行きたいと思ってます。

N.H
GlueAnchor®の技術はまだまだポテンシャルがあるんですね。
デザイン性だったり、ちょっと角度を変えてリサイクル性とか。
当時なかった多角的なアプローチができるような話も拡げていける可能性はあるので、そういうものをもう少しスケールアップしていくことも大事だと思います。
当たり前の技術とか標準技術にして行くみたいなところも視野に入れて、これを拡張させていくっていうのをやって行きたいなって言うのが今の想いですね。
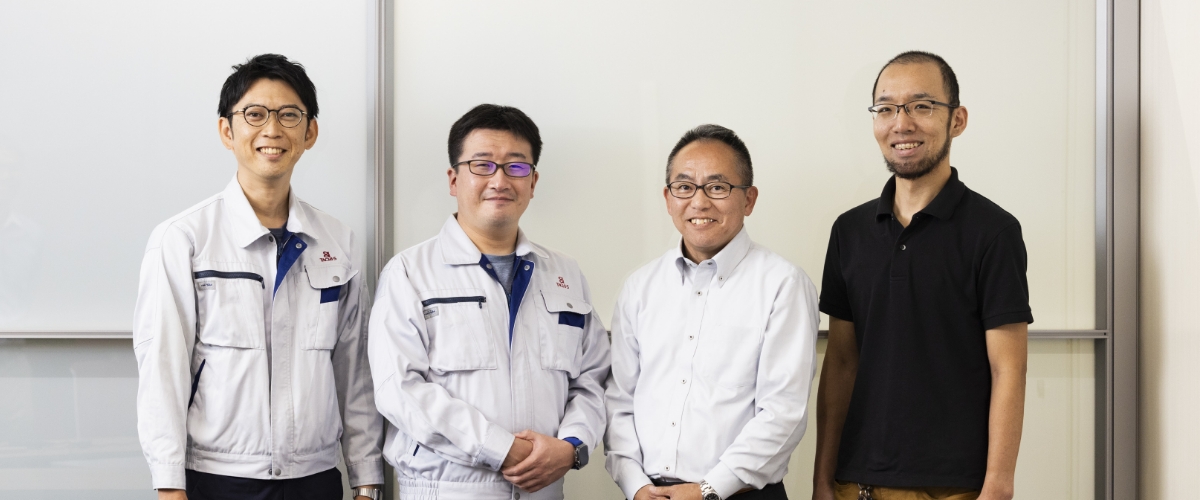
Fin
※用語
インテグラ:車の名前 今回の主要テーマである「GlueAnchor®」という技術を使ったシートが搭載されている。
アキュラ:Honda社が北米で展開しているパフォーマンスブランド名。
GlueAnchor®:トリムカバーとパッドを組み付けるタチエス独自の部分接着工法。外観品質、軽量、パッド薄型化、座り心地向上に効果がある。
社員インタビューに戻る